Hydroforming
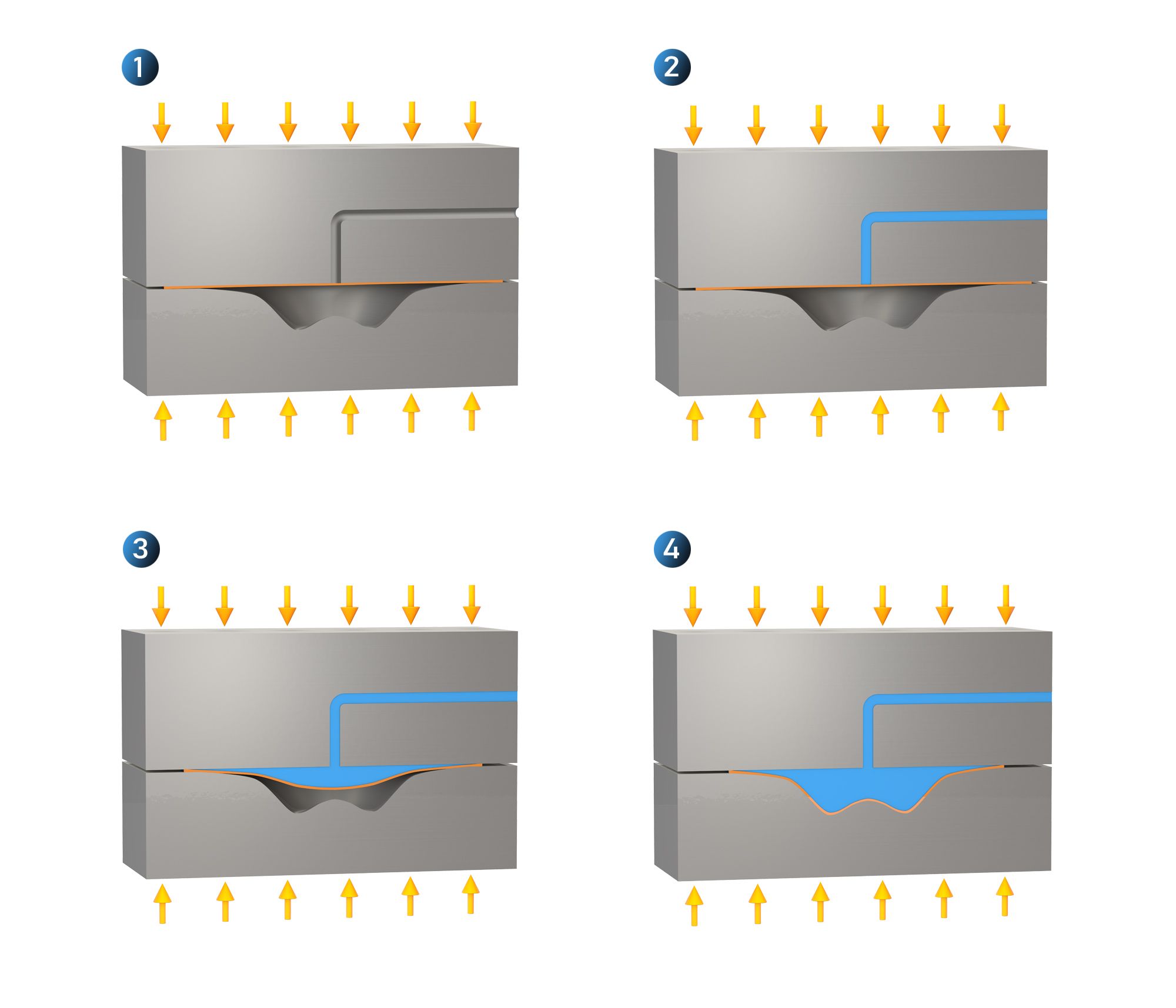
What is hydroforming?
Hydroforming is a forming process in which material is pressed into a desired shape under high pressure using an active medium (e.g. water-oil emulsion). A distinction is made between hydroforming under internal pressure and hydroforming under external pressure. While hydroforming under internal pressure is mainly used to form pipes, hydroforming under external pressure is mainly used to form sheet metal.
Both processes are possible with the FormBalancer hydroforming machine. In contrast to other hydroforming approaches, Fluid Forming does not require a membrane for a safe forming process. This extends the forming limits in order to produce complex formed parts from sheet metal.
How does hydroforming work with the FormBalancer?
Hydroforming with the FormBalancer is a high-pressure forming process in which metal blanks are formed into a desired geometry under high pressure with the help of a fluid. Hydroforming is similar to conventional deep drawing with a counter mold. The special difference to conventional technology is that instead of a stamp, forming is carried out with an active medium. Medium pressures of up to 4000 bar are required for this forming process, which means, depending on the component size, that very high mold closing forces have to be applied.
The desire of many component designers and designers to implement this technology has so far failed because of suitable forming machines with which this specialized hydroforming technology could be implemented. The FormBalancer opens up a wide range of applications in various sectors such as automotive, aerospace, medical technology and many others where complex components have to be manufactured with high precision and quality.
What advantages does hydroforming offer over deep drawing?
Hydroforming is similar to conventional deep-drawing, but has significant advantages in terms of the molded part and tool costs or component manufacturing costs. The FormBalancer creates many attractive possibilities with cost-effective implementation processes. We can produce special products for every industry. See for yourself.
Hydroforming advantages at a glance:
-
Tool cost savings of up to 80%
-
Very short development time of 6-8 weeks for new prototypes (rapid prototyping)
-
Highest surface quality (dimensional accuracy, low residual stress, homogeneous sheet thickness distribution and use of brushed and coated materials)
-
Implementation of the most complex geometries
(Undercuts, free-form surfaces, counter geometries, etc.) -
All cold-formable materials can be used
(depending on the material 0.05 – 8 mm) -
Resource-saving use of materials
Low stress and springback during hydroforming
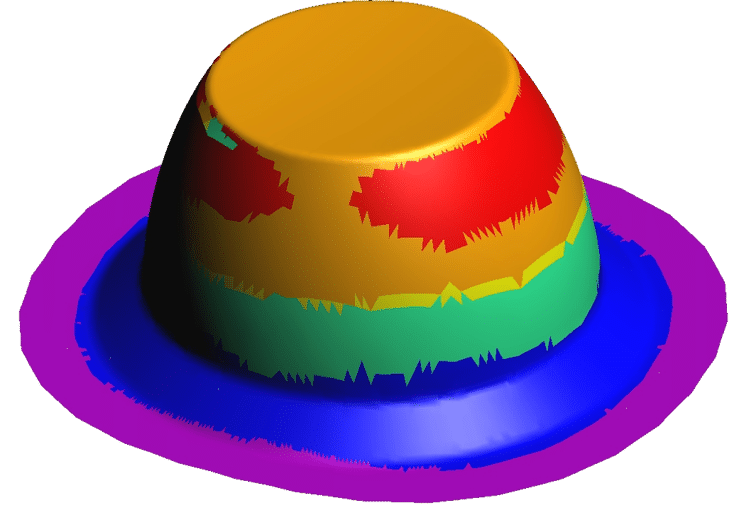
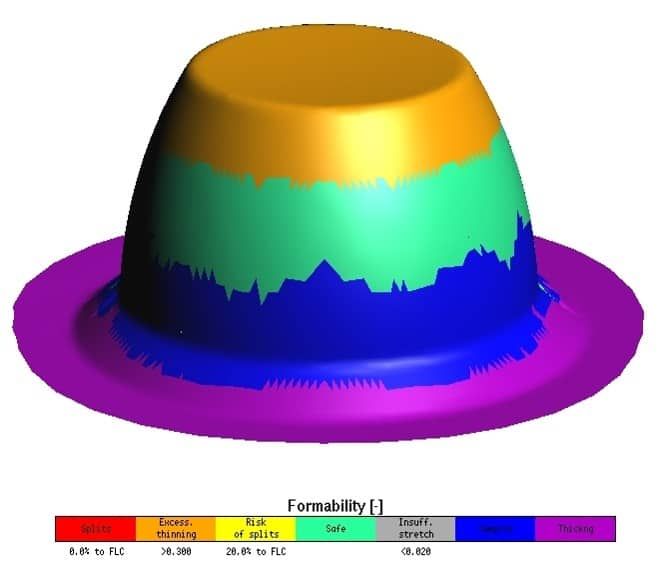
-
Homogeneous strength and rigidity
-
Avoid abrupt voltage transitions
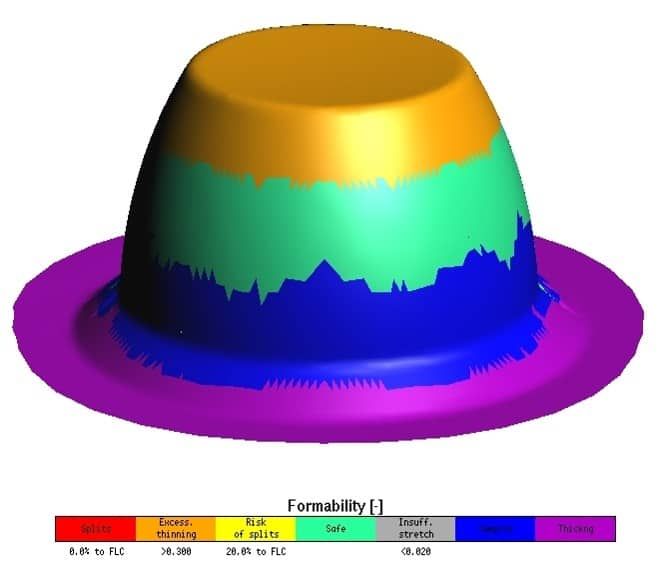
Dimensional stability through hydroforming
-
Highest repeatability
-
especially with complex geometries
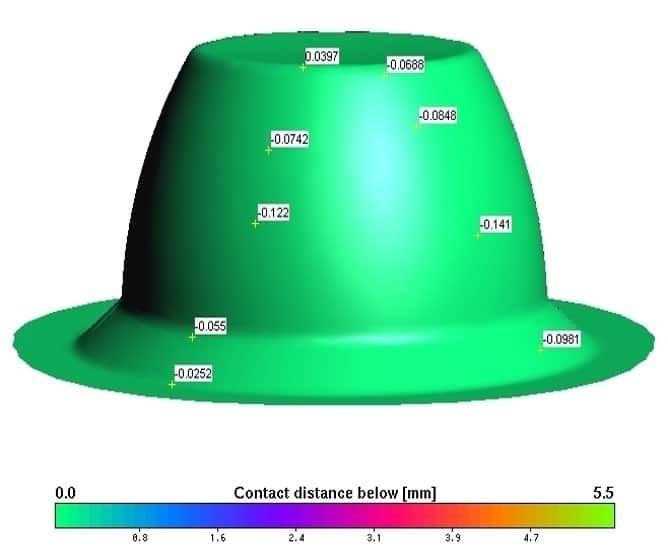
Realization of different materials, sizes and sheet thicknesses with Fluid Forming

Which industries benefit from the use of hydroforming?
The advantages of hydroforming can be used in almost all industries. Companies are constantly faced with the challenge of reconciling cost savings and innovative solutions for the further development of their products. Our high-pressure forming technology opens up attractive possibilities in terms of price/performance ratio and the timely realization process.
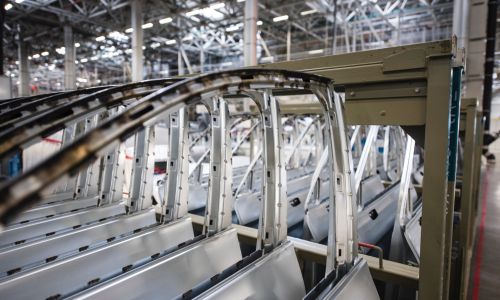
Automotive
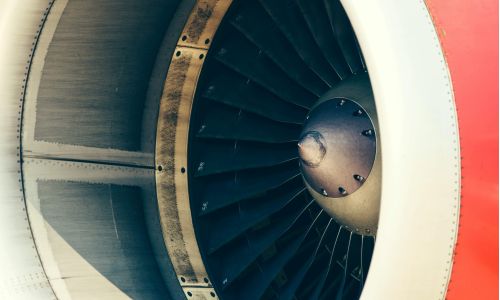
Aerospace
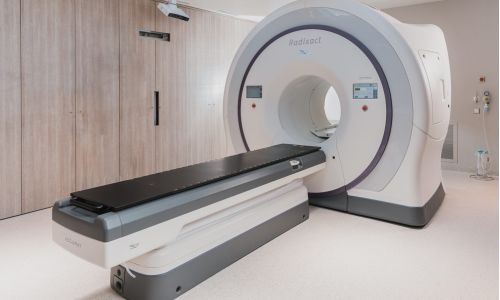
Medical technology
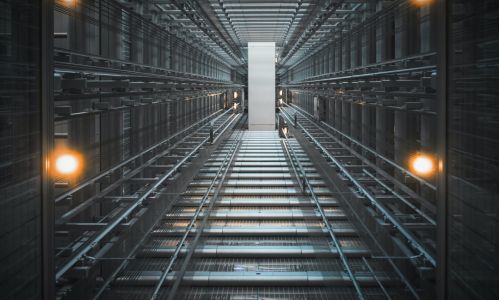
Electrical engineering
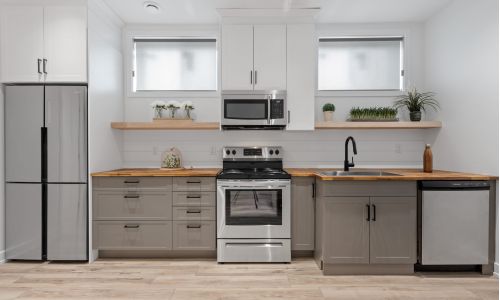
Household technology
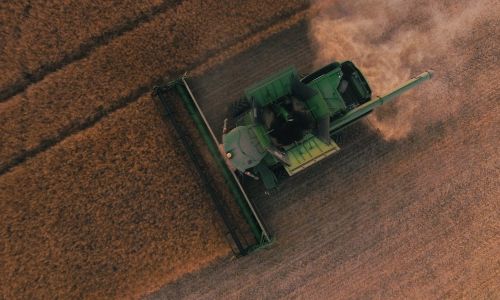